Prunt Board 2
Features
- 6× TMC2240 stepper drivers, all capable of running at 3A with minimal airflow.
- 2× 20A heater outputs.
- 4× fan outputs, supporting up to 2A 4-pin fans or 500mA 2-pin fans.
- 4× thermistor inputs supporting PT1000 and most common NTC thermistors.
- 4× endstop inputs.
- 40A maximum input current at 12-24V.
- Fully isolated USB to protect upstream devices.
- Reverse polarity protection.
- Protection against electrical shorts to 24V on most exposed pins.
- Hardware generated step generation at up to 2.54MHz (limited by TMC2240) with 128 velocity levels updated at 20kHz.
- Fail-safe firmware updates, eliminating the need to ever install a jumper.
- Hardware counters for high-speed fan tachometers.
- Soft-start, allowing for a wider range of power supplies.
Size and Connector Positions
Connectors
USB
- The USB port connects to and powers a 6Mb/s USB-UART adaptor with an isolated connection to the rest of the board.
Power
- The power supply screw terminals support solid or stranded wires from 6-20AWG / 0.5-10mm² and must be torqued to 1.2Nm.
- The board contains reverse polarity protection to prevent against accidental miswiring; however, applying AC or quickly switching between polarities will destroy the board.
- The board may be powered from a 12-24V power supply.
- Maximum current must be limited to 40A with an external components if the power supply is capable of continuously supplying over 40A.
- The board may not power on if the power supply voltage is over 27V or under 8.3V. The 27V cutoff does not imply that a power supply voltage over 24V is supported.
- The board contains a soft-start circuit so no large load will be applied to the power supply at power-on.
Steppers
- The numbers above the stepper ports correspond to the numbers in the GUI.
- Note that the stepper pinout is different from some other boards, specifically each stepper phase should be connected to two adjacent pins.
Switch Inputs
- Each input pin is pulled high by a 4.7kΩ resistor with a series diode.
- Input pins are protected from overvoltage inputs.
- The 4-6V pin will only rise above approximately 5V in the event of an overvoltage event on the board (including some events not on the switch input pins).
- Overvoltage on a 4-6V pin will cause all other 4-6V pins to rise to the applied voltage but will not cause damage to the board itself.
- Power and ground pins are otherwise protected, pay careful attention to the pinout to ensure that the power pins are not shorted to ground.
- Total current draw must be limited to 500mA.
- Minimum negative-going threshold voltage: 1.5V for 800Hz bandwidth with 50% duty cycle square wave.
- Maximum positive-going threshold voltage: 3.5V (or pull-up) for 800Hz bandwidth with 50% duty cycle square wave.
ADC Inputs
- One side of each ADC input is pulled to 3.3-3.6V via a 2kΩ resistor.
Fans
- Each fan power pin is protected by a replaceable fuse (2A by default).
- Ground pins are not protected.
- PWM pins are protected by a smart low-side load switch.
- PWM pins are capable of driving 500mA each and may be used to directly drive a 2 pin fan.
- PWM pins may operate from 1Hz to 50kHz.
- The PWM pins operate in a slow decay mode with a diode to 24V when driving inductive loads.
- 3 pin fans are not supported unless they are not driven by the PWM pin or the tachometer pin is left disconnected.
- The board contains jumper pins for pulling each PWM pin to 4-6V for obscure fans that may require this.
- Each tachometer pin is pulled high by a 4.7kΩ resistor with a series diode.
- Tachometer minimum negative-going threshold voltage: 1.5V for 800Hz bandwidth with 50% duty cycle square wave.
- Tachometer maximum positive-going threshold voltage: 3.5V (or pull-up) for 800Hz bandwidth with 50% duty cycle square wave.
Heaters
- The heater screw terminals support solid or stranded wires from 12-26AWG / 0.2-4mm² and must be torqued to 0.5Nm.
- Each heater power pin is protected by a replaceable fuse (10A and 5A by default).
- Switched ground pins are not protected.
- Heaters may switch up to 20A.
Flashing
Main MCU
The main MCU can be automatically updated by the Prunt server and should never need to be flashed manually while running Prunt, however it is still possible to do so by installing one of the included jumpers on the pins marked as BOOT0.
Secondary MCU
We do not prohibit the use of third-party firmware; however, due to the fact that we can not audit it, the user assumes full responsibility for any hardware damage that may occur as a result of installing or using third-party firmware.
In addition, any damage caused while attempting to flash the secondary MCU is also the responsibility of the user as the secondary MCU is not designed to be flashed by the user.
The secondary MCU on the USB side acts as a USB-UART bridge and should never need to be updated however it is possible to do so.
When the MCU is placed in to system memory boot mode the USB connector becomes a UART connector, therefore an adaptor is required. Some early units may include an adaptor. If building an adaptor, connect the TX pin (input pin on STM32) to D+ and the RX pin (output pin on STM32) to D-.
To flash the MCU:
- Disconnect all power and unplug the USB port.
- Plug a USB cable which is disconnected at both ends in to the Prunt board.
- While shorting the two pads circled in the below image with a sharp pair of tweezers, plug the other end of the USB cable in to a powered adaptor.
- Use stm32flash or your preferred tool to flash the new firmware.
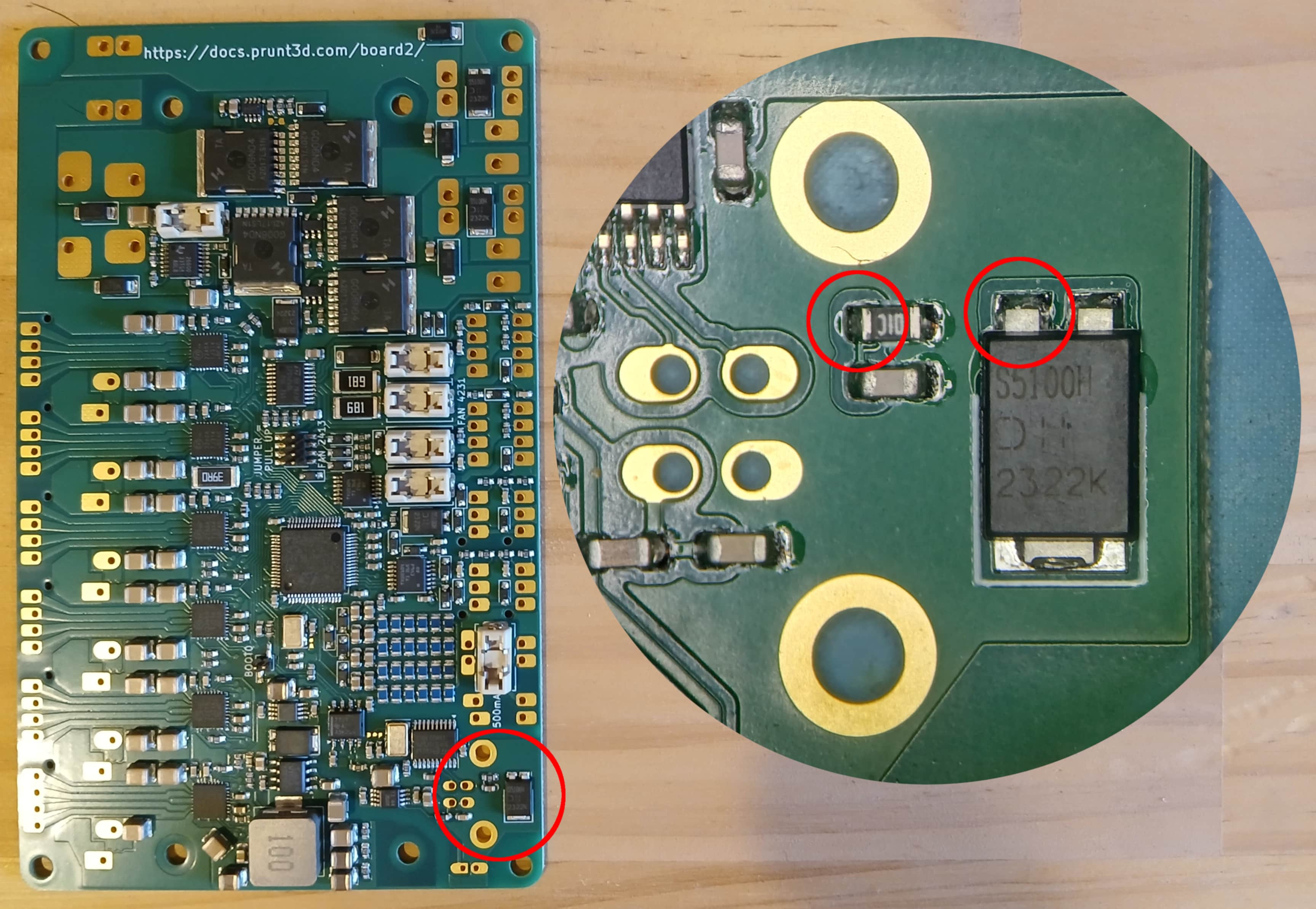
Klipper/Kalico
A custom version of Klipper/Kalico is currently required on this board as upstream Klipper/Kalico does not support the following features:
- HSE clock bypass mode (PR awaiting merge).
- Soft start support (no PR as the code is specific to this board).
A Kalico firmware image is embedded in the Prunt firmware and can be switched to by appending --reboot-to-kalico
to the prunt_board_2_server
command.
This firmware is also currently compatible with Klipper.
Basic Setup
Below are the approximate steps for setting up a printer with a Prunt board:
- Connect the board to the various motors/thermistors/etc., noting the labels on the board where each is connected.
- Power on the board and run the server binary on the host machine (for Prunt Board 2 it can be downloaded from https://github.com/Prunt3D/prunt_board_2_software/releases). Note that a command line argument specifying a serial port is required for some boards (
--serial-port=/dev/serial/by-id/usb-Prunt_3D_Prunt_Board_2_…
for Prunt Board 2, where … is replaced with the path for your board). - Navigate to <host_address>:8080 in a web browser.
- Navigate to “Config Editor” at the top of the page.
- Go through each tab and configure the board as desired using the built-in descriptions.
- Finally navigate to the Prunt tab in the config editor and tick the box to enable Prunt and save.
- Restart the server binary.
It is also heavily recommended to set up CPU isolation for a single CPU which is then passed to the --prunt-step-generator-cpu=
command line argument.
For Prunt Board 2 an additional CPU should be isolated and passed to --communications-cpu=
.
CPU Isolation
CPU isolation prevents any tasks from running on a given CPU if they are not assigned to that specific CPU. This is useful for Prunt as it can prevent other tasks from taking away resources from the time-sensitive step generator task.
Example of parameters to isolate the third and fourth CPU: nohz=on nohz_full=2,3 rcu_nocbs=2,3 isolcpus=nohz,domain,managed_irq,2,3 rcu_nocb_poll
To add these parameters on OpenSUSE or SUSE: Run yast2
, navigate to boot loader > kernel parameters
, and append the parameters to the existing parameters.
To add these parameters on Raspberry Pi OS: Edit /boot/cmdline.txt
and append the parameters to the existing parameters.
Note that CPUs in Prunt start from 1 whereas CPUs in Linux start from 0, therefore for the above parameters 3 or 4 should be passed to Prunt rather than 2 or 3.